Introduction
Silicon is the cornerstone of the semiconductor industry. From microchips and photovoltaic cells to MEMS and sensors, silicon’s role is irreplaceable. However, this brittle yet hard material presents a significant challenge when it comes to slicing and shaping — especially when high yield and flawless surfaces are crucial. With traditional cutting techniques reaching their limitations, the diamond wire has emerged as a game-changing solution.
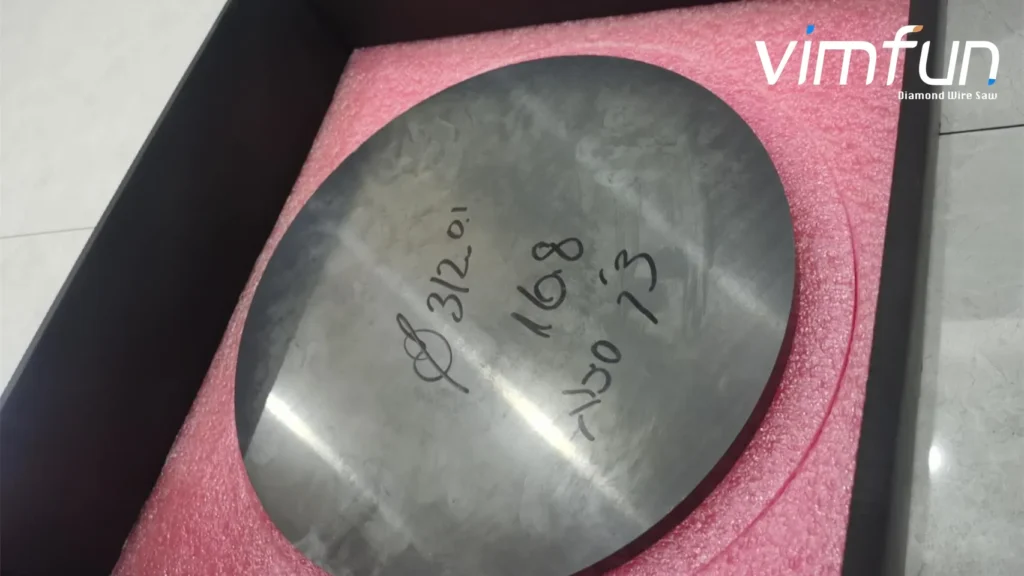
The Challenge of Cutting Silicon
Silicon is both hard and fragile, requiring cutting tools that can deliver extreme precision without inducing micro-cracks, stress damage, or excessive material loss. Traditional mechanical sawing or slurry-based wire cutting methods often struggle with consistency, slow throughput, and significant kerf loss — a problem especially critical when working with expensive silicon wafers.
This challenge has led to the adoption of diamond wire as an advanced cutting technology designed for high-precision material processing.
Why Diamond Wire is Ideal for Silicon
Diamond wire is a fine, tensioned metal or resin-coated strand embedded with industrial-grade diamond particles. These synthetic diamonds, known for their exceptional hardness, act as miniature cutting tools during high-speed slicing operations.
What makes diamond wire especially effective for silicon processing includes:
- Minimal Material Loss: With a very narrow kerf width, diamond wire maximizes the usable surface of each silicon ingot, reducing waste.
- Superior Edge Quality: The clean, low-damage cut leaves behind smoother surfaces, reducing the need for post-processing like polishing.
- Faster Processing Times: The high efficiency of diamond-based abrasion allows for quicker slicing, increasing throughput and productivity.
- Better Yield Rates: Lower mechanical stress leads to fewer defective wafers, which translates into better production results.
Applications Across the Semiconductor Sector
The use of diamond wire in silicon cutting has expanded rapidly across various high-tech industries. Key applications include:
- Solar Energy: Slicing monocrystalline and polycrystalline silicon blocks into ultra-thin wafers for solar cells.
- Microelectronics: Precision cutting of silicon for integrated circuits and microprocessors.
- Power Devices: Preparing high-purity silicon substrates used in high-voltage or high-frequency applications.
- R&D and Advanced Materials: Fabrication of silicon-based components in emerging tech like photonics and quantum computing.
Cleaner and More Sustainable
Compared to older abrasive cutting methods, diamond wire processing produces less dust, slurry, and environmental contamination. The clean-cutting nature also reduces cooling fluid usage and simplifies waste management, aligning well with sustainable manufacturing goals.
Looking Ahead
As the demand for ultra-thin, high-performance silicon components grows, manufacturers are under pressure to enhance precision while cutting costs. Diamond wire is perfectly positioned to meet this demand by offering consistent, high-quality results across a variety of silicon-based applications.
Conclusion
So, can diamond wire cut silicon? Not only can it — it does so with outstanding efficiency, accuracy, and environmental benefits. As the semiconductor industry evolves, diamond wire cutting is proving to be the optimal solution for shaping the future of silicon materials.